Du hast Fragen? Wir haben Antworten!
Lorem ipsum dolor sit amet consectetur. Sollicitudin dolor massa sagittis elit nunc eleifend commodo.
Wir verarbeiten nur die Daten, die von Ihrer Maschine kommen, entweder lokal in Ihrem Betrieb oder auf einer Cloud-basierten Infrastruktur, die in Ihrer Anwendung gehostet wird und einen verschlüsselten Datenverkehr beinhaltet. Für weitere Informationen zum Thema IT-Sicherheit und Datenschutz können Sie uns gerne kontaktieren.
Das Wissen und die Erfahrungen der Mitarbeiter:innen (Instandhaltung, Bediener:innen, Prozessexpert:innen etc.) werden situativ “on-the-fly” über Smartphone/Smartwatch/Tablet gesammelt, um ihr Expertenwissen als neue Lösungen für dedizierte Probleme zu verknüpfen. Auf diese Weise können Lösungen vorgeschlagen werden, wenn die entsprechende Ursache auftritt. Die Bediener/-innen können über das Smartphone oder die Smartwatch Texte, Bilder mit Markierungen oder kurze Videos zur Lösung hinzufügen.
Die plus10 Software Tools bieten bidirektionale Schnittstellen, entweder durch gemeinsame Nutzung einer Datenbank oder durch native Protokolle zu benachbarten IT-Systemen. Wir können z.B. kontinuierlich berechnete KPIs zur Leistung und zu den Ursachen austauschen und Ihre Planungs-, Ist- und Soll-Zahlen in Echtzeit und objektiv aktualisieren. Ihre Produktionsplanung und -steuerung wird durch das Feedback von Darwin, Hopper und Shannon® deutlich präziser.
Wir unterstützen derzeit verschiedene SPS/NC-Typen. Informieren Sie sich hier über die von uns unterstützten Steuerungen oder fragen Sie uns nach der Kompatibilität zu Ihrem MES-/ERP-System.
Shannon® ist für die folgenden Geräte und Betriebssysteme verfügbar:
- Android Smartphones über Google Playstore
- iOS Smartphones oder iPods über App Store
- Apple Watch (watchOS) über App Store
- Web-Browser
Die Shannon®-App kann entweder auf einzelne Geräte heruntergeladen oder über ein Mobile Device Management (MDM) zentral verwaltet werden.
plus10 erfasst die Daten direkt von allen integrierten Maschinensteuerungen (SPS, NC), Robotersteuerungen (RC), etc. einer Produktionsmaschine oder von allen in einer Produktionslinie integrierten Steuerungen. Dazu nutzen wir unseren plus10 DataCollector, um die Daten in hoher Frequenz von allen beteiligten SPS, NC und/oder RC zu erfassen. Bislang können wir hochfrequente Maschinendaten mit verschiedenen herstellerspezifischen SPS-Protokollen erfassen und wir fügen kontinuierlich weitere Steuerungen hinzu. Informieren Sie sich hier über die von uns unterstützten Steuerungen oder fragen Sie uns nach der Kompatibilität zu Ihrem speziellen Steuerungstyp.
Falls Sie bereits eine leistungsfähige IT-Infrastruktur in Ihrer Fabrik installiert haben, bieten wir auch die Anbindung an Ihre Middleware an.
Grundsätzlich erfasst und verarbeitet plus10 alle Daten der Maschinensteuerung (SPS) der Produktionsmaschinen oder der Produktionslinie in hoher Frequenz. Die hohe Abtastrate (wir sprechen von Millisekunden) ist notwendig, um die Ursachen von Problemen und nicht nur deren Folgeerscheinungen zu erkennen und zuzuordnen. In einigen Fällen werden zusätzlich die RC- und NC-Daten von z.B. Handlingrobotern benötigt. Im Standardfall müssen keine zusätzlichen Sensoren oder Kameras installiert werden.
Die plus10 Software-Tools sind flexibel in Bezug auf die IT-Infrastruktur. Die Datenerfassung und Vorverarbeitung läuft kontinuierlich lokal, z.B. auf einem Industrial Edge Device oder einer virtuellen Maschine innerhalb des Maschinensteuerungsnetzwerks. Für den nächsten Verarbeitungsschritt passt sich plus10 an Ihre bevorzugte Lösung an: Wir können eine Cloud-Umgebung für unsere Software-Tools anbieten oder sie werden auf einer virtuellen Maschine on-premise in Ihrem bestehenden werksinternen Rechenzentrum ausgeführt. Beides ist möglich und wir haben Erfahrung mit beiden Optionen.
Nein, das ist kein Problem. Sie finden hier alle Maschinensteuerungen, die derzeit kompatibel sind.
Ihre SPS sind noch nicht aufgeführt? Setzen Sie sich mit uns in Verbindung, um mit unserer Softwareentwicklung die Einführung von neuen Schnittstellen zu klären.
Die plus10-Kosten sind in zwei Pakete unterteilt: das einmalige Onboarding, das die Erstinstallation, die Konfiguration und den Go-Live umfasst. Danach gibt es eine jährliche Lizenzgebühr für unsere Software-Services. Die Jahreslizenz beinhaltet Updates und Standardsupport. Beides ist abhängig von der Anzahl und Art der integrierten Maschinensteuerungen und der Komplexität der Produktionsmaschinen bzw. der Produktionslinie.
Shannon®, Hopper und Darwin sind als Software-as-a-Service verfügbar und werden auf Microsoft Azure im plus10-Abonnement gehostet. Darüber hinaus kann unsere Software in einer kundenspezifischen Cloud-Infrastruktur oder als On-Premise-Lösung betrieben werden.
Für Shannon® gibt es Apps für Android und iOS (inkl. watchOS).
Unsere jährliche Lizenzgebühr beinhaltet Standard-Support und Software-Updates auf die neueste Version des/der bestellten Software-Service(s). Mit einer plus10 Softwarelizenz von Darwin, Hopper oder Shannon® garantieren wir Ihnen also die neueste, effizienteste und benutzerfreundlichste Version unserer Optimierungssoftware. Dabei betreuen wir weltweit Produktionsanlagen, in denen unsere Software Tools installiert sind.
Dies hängt von der Art der Maschinensteuerung (SPS) und der vorhandenen IT-Infrastruktur ab. Wenn die Konnektivität zu allen SPS besteht und Sie die Recheninfrastruktur bereitstellen (entweder als lokale virtuelle Maschine oder als dezidierter Server), kann die Installation und Konfiguration remote durchgeführt werden. In diesem Fall wird die Schulung des Bedienpersonals auf Shannon®, Hopper oder Darwin immer noch vor Ort durchgeführt, kann aber als Video-Schulung virtualisiert werden, auch im Falle von pandemischen Schließungen oder Zugangsbeschränkungen.
Alle plus10-Software Tools dienen der Bewältigung eines hohen Komplexitätsgrads in der Produktion im Mehrschichtbetrieb.
Je nach Bedarf können Sie ein geeignetes plus10-Tool auswählen, um Ihre spezifischen Produktionsprobleme zu bewältigen:
- Shannon® hilft Ihnen bei Störungen und technischen Ausfällen. und optimiert so die technische Verfügbarkeit.
- Darwin erkennt kontinuierlich Leistungsgrad-Optimierungspotenziale während des Betriebs – entweder in verketteten und automatisierten Prozessketten oder bei mindestens 6 gleichen Einzelmaschinen. Diese Maschinen oder Produktionslinien können auch in verschiedenen Werken auf der ganzen Welt stehen.
- Hopper senkt Ihre Ausschussrate in Kombination mit der Zykluszeit. Das heißt Hopper hilft, hohe Ausschussraten oder Konformitätskosten zu reduzieren und optimiert so die Qualität.
Alle plus10-Softwaretools können nur auf vollautomatisierten Produktionsmaschinen oder Produktions-/Montagelinien eingesetzt werden, da ein automatischer Dateninput aus jedem Prozessschritt erforderlich ist. Die Bediener/-innen übernehmen in der Regel logistische und unterstützende Aufgaben wie das Befüllen oder die Entnahme von Material sowie statistische Prozesskontrollen und die Fehlersuche im Falle von Problemen.
Jetzt Kostenlose Problem-Evaluation anfragen.
- Produktvorstellung mit Demo
- Roadmap zur Problemlösung
- Ganzheitliche Bewertung des Ansatzes
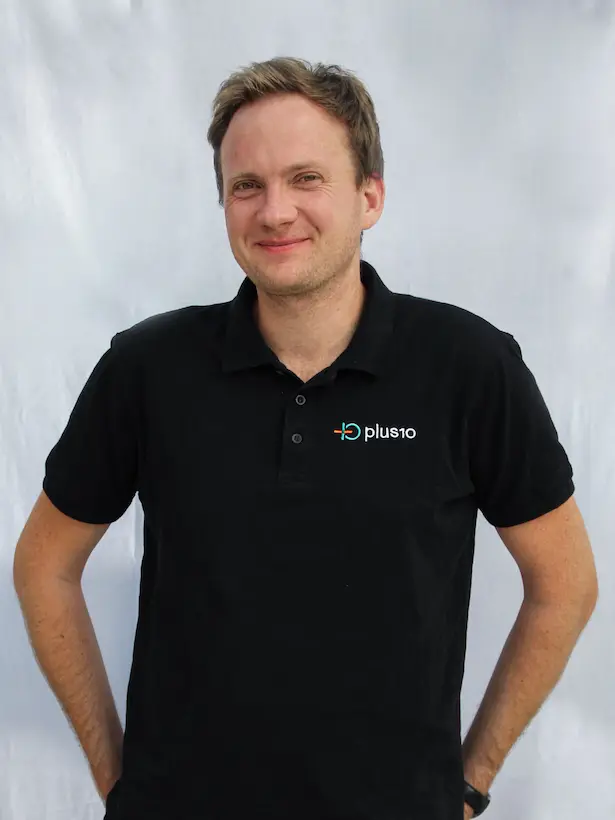