Erfolgsgeschichten im Pharma- und Medizin-technikbereich
Optimieren Sie Ihre Fertigung mit kontinuierlich lernender und situativ handelnder Software
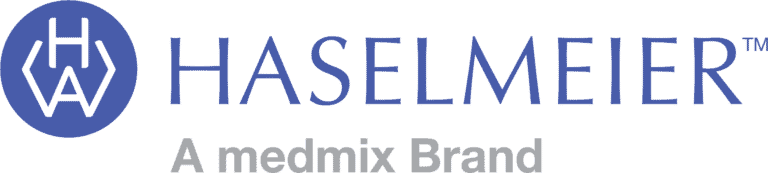
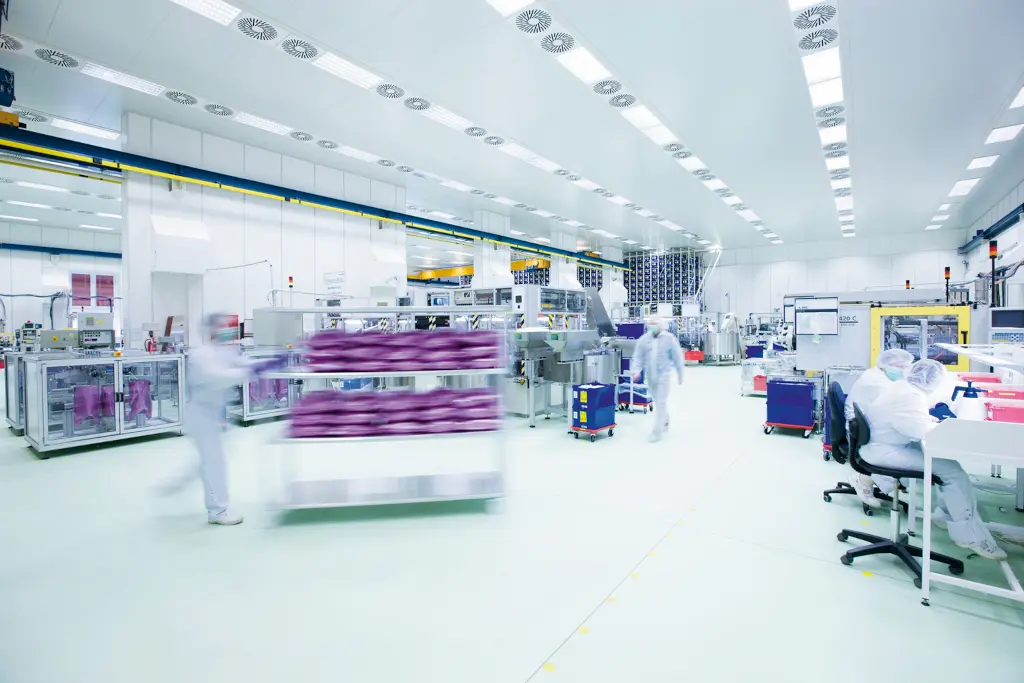
Bieten Sie Ihren Kunden digitale Software-Tools an, um die Produktivität Ihrer Fertigungsanlagen zu steigern
plus10 Analytics Software identifiziert Probleme und Optimierungspotentiale auf Basis von hochfrequenten Maschinendaten. Mit der Integration in Ihre Anlagen bieten Sie einen echten Mehrwert.
Komplexe Fertigungsanlagen effizient zu betreiben ist eine Herausforderung
Neben der Produktmodularisierung und Standardisierung spielen digitale Innovationen eine wichtige Rolle in ihrem Produktportfolio. Endkunden fordern z.B. digitale Dienstleistungen und digital erweiterte Maschinen, welche
- komplexe Support-Anfragen besser und transparenter lösbar machen
- die Betriebseffizienz optimieren und
- die Verfügbarkeit der Maschinen durch datengesteuerte Technologien garantieren.
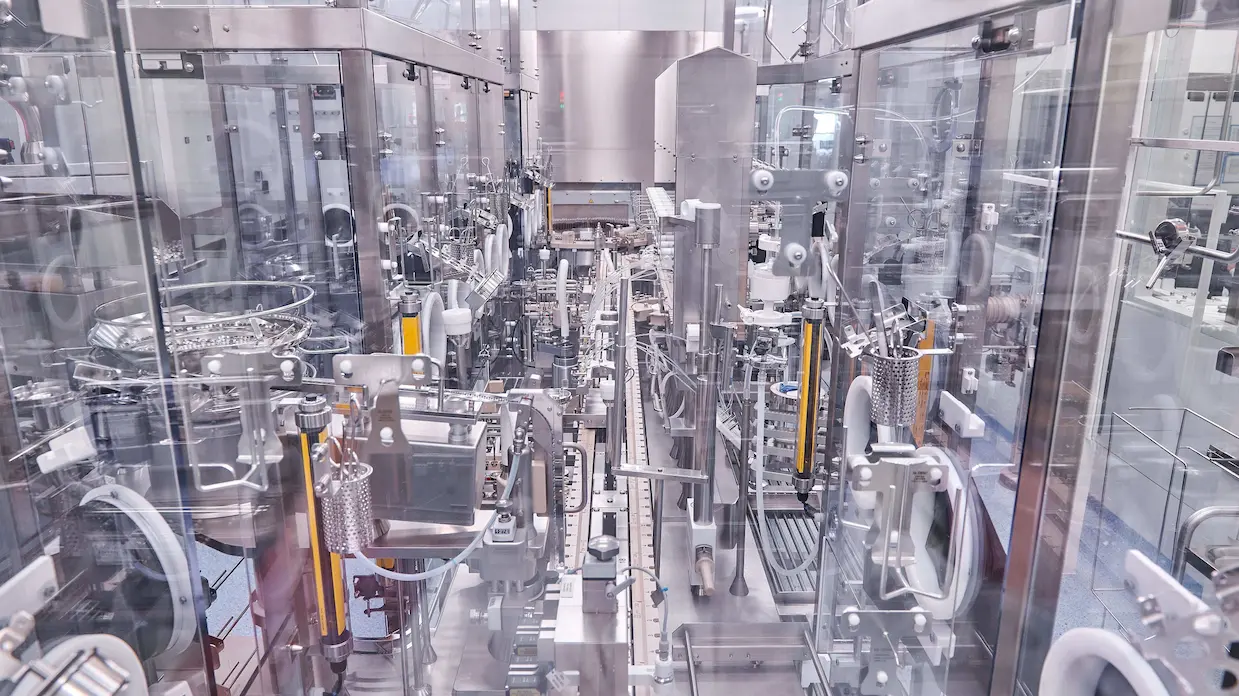
Optimierung von Fertigungsanlagen als digitaler Service
Integrieren Sie plus10 Softwareprodukte in Ihre Fertigungsanlagen und bieten Sie so Ihren Kunden einen Mehrwert beim effizienten Betrieb Ihrer Maschinen und Fertigungslinien.
- Shannon gibt passgenaue Vorschläge zur Behebung auch von komplizierten Störungen
- Darwin schafft Transparenz über Maschinenverhalten: So verstehen Sie was passiert ist - auch remote
- Optimierung von Engpässen und Störungen während der Inbetriebnahme
_IMB.webp)
Das sagen unsere Kunden & Partner
Vorteile im Pharma- und Medizintechnikbereich
5-15%
Steigerung der OEE durch Reduzierung der Stillstandzeiten (MTTR)
Bis zu 38 %
Reduzierung der durchschnittlichen Produktivitätsschwankung
10 – 30 %
Verkürzung der Anlauf- und Verlagerungsphase
Softwarelösungen - gemacht für Ihre Branche
- Unsere Optimierungswerkzeuge sind so konzipiert, dass sie die GMP-Standards (Good Manufacturing Practice) erfüllen. Dabei berücksichtigen wir den risikobasierten Ansatz des EU-GMP Annex 11, den praxisnahen GAMP 5 Leitfaden sowie die Verfahren der Computerized System Validation (CSV).
- Generierte Vorschläge und Maßnahmen werden GMP/FDA-konform dokumentiert
- Auditierung von Änderungen und wichtigen Events
- Optionaler Freigabeprozess beim Hinzufügen neuer Störungsmaßnahmen im System (Vier-Augen-Prinzip)
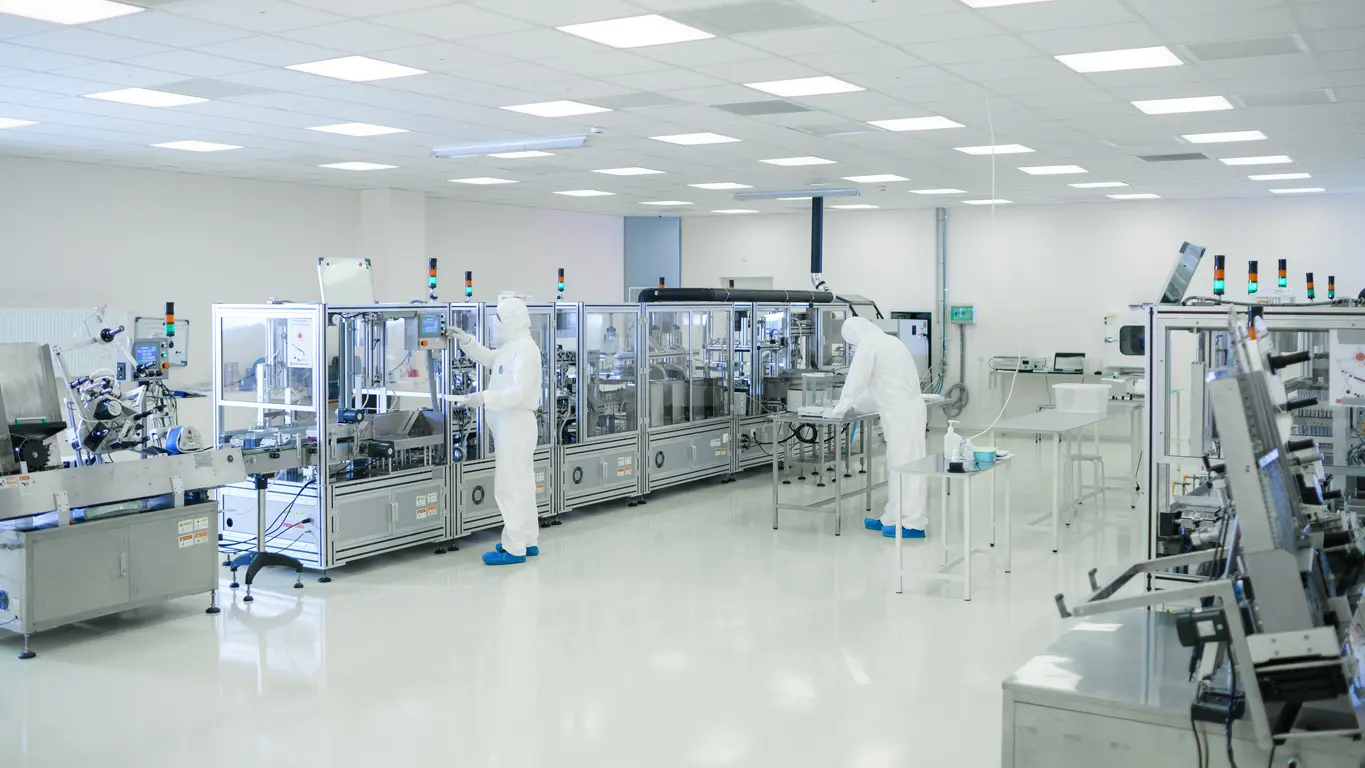
Mit unseren Produkten zum Erfolg im Maschinen- und Anlagenbau
Unsere Analyse-Software adressiert die drei OEE-Verlustkategorien technische Verfügbarkeit, Leistungsgrad und Qualität.
Darwin - Ursachen für Performance-Verluste identifizieren
- Decken Sie Engpässe in Ihren Fertigungsanlagen auf und schaffen Sie Transparenz über die Ursachen von Performance-Verlusten - bis hinunter auf Signalebene.
- Erhöhung der Output-Rate pro Maschine durch Reduzierung der Zykluszeit
- Erklärung, warum ähnliche Maschinen in der gleichen Fabrik unterschiedlich funktionieren
- Trends in Störungs- und Prozesszeit-Daten frühzeitig erkennen und so zeitnah Optimierungen durchführen
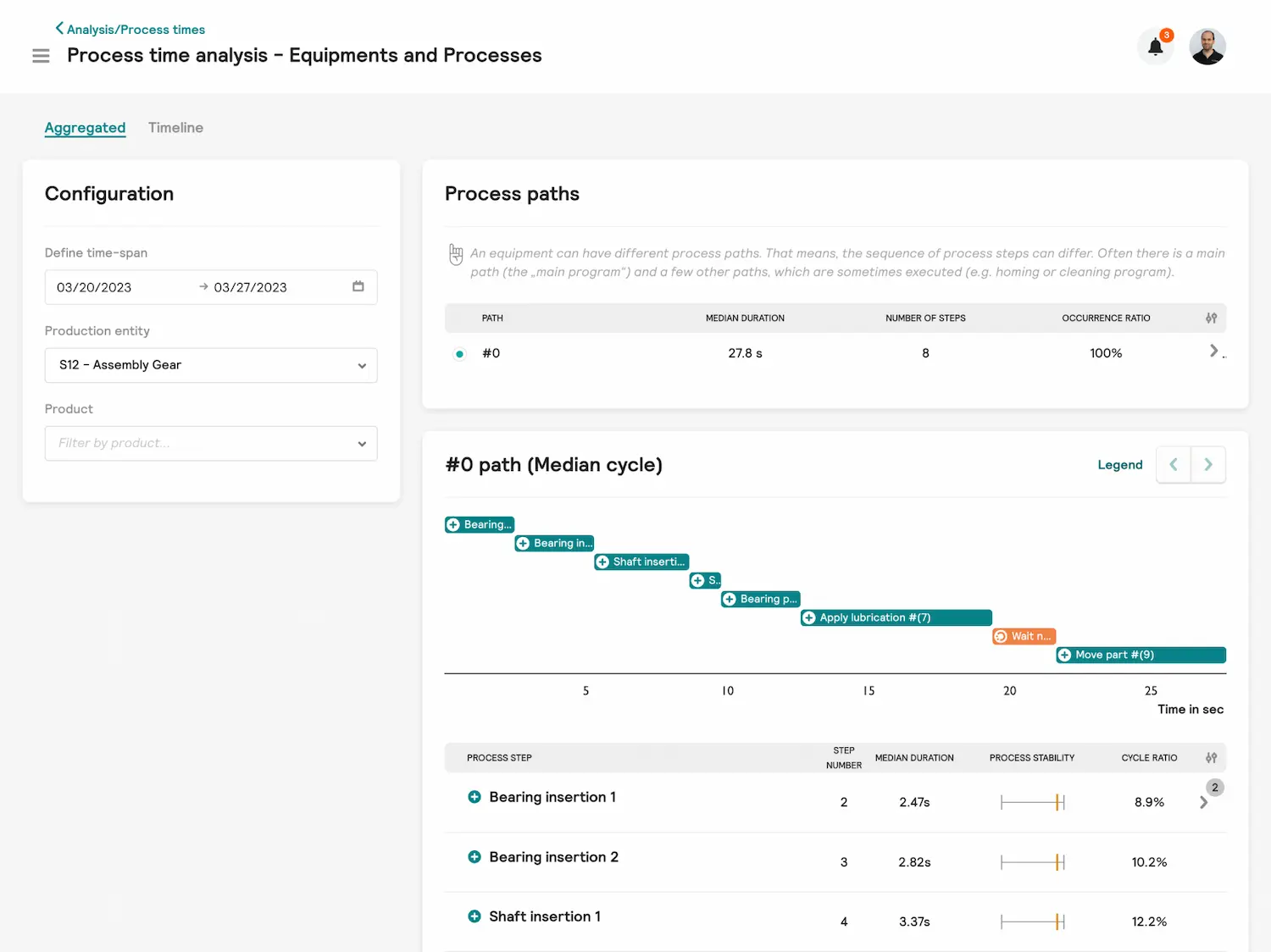
Shannon® - die operative Shopfloor-Assistenz
- Machen Sie Ihre Anlagenbediener zu Experten: Shannon® informiert über Störungsursachen mit situativen Lösungsvorschlägen und reduziert so Stillstandszeiten durch intelligentes Wissensmangement
- 5 – 15 % Steigerung der OEE durch Reduzierung von Ausfallzeiten und Troubleshooting (MTTR)
- Wissensmanagement: Aufbau von Wissen über das tatsächliche Maschinenverhalten und Lösungen
- Fachkräftemangel adressieren: Sofortige Unterstützung bei der Problemlösung durch Vorschlag des Expertenwissens
.webp)
Hopper - der Qualitätsoptimierer
- Mit automatisch generierten Vorschlägen zu Parameter-Optimierungen reduzieren Sie Ausschuss und Zykluszeit im Spritzgießprozess.
- Erhöhung der Output-Rate durch deutliche Reduzierung von Ausschuss und Zykluszeit
- Empfehlungen zu detaillierten Parameteranpassungen unter Berücksichtigung aller Einflussfaktoren auf den Prozess
- Situative und automatisierte Empfehlungen auf Smartwatch, Smartphone und Browser verfügbar
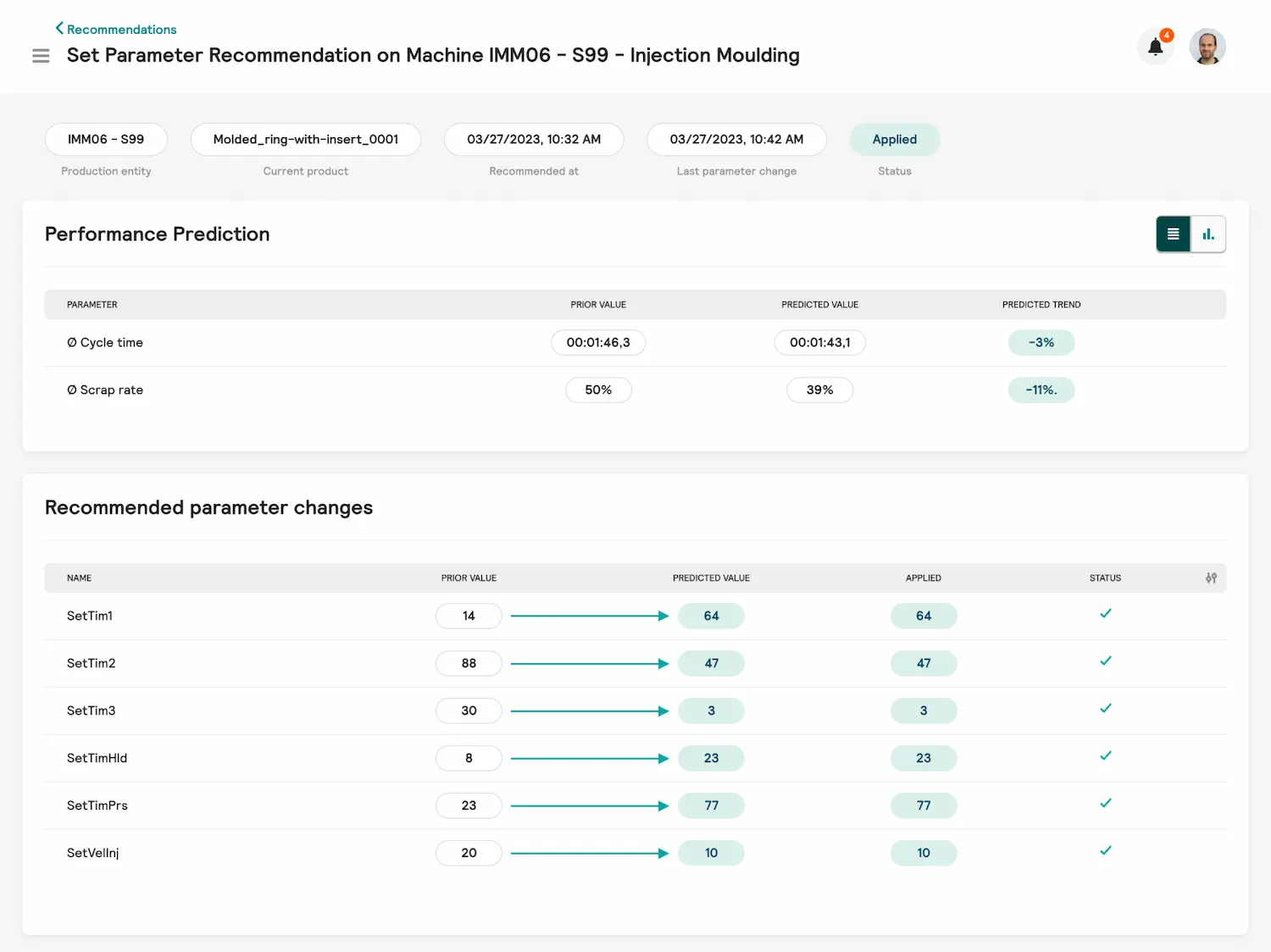
Jetzt Kostenlose Problem-Evaluation anfragen.
- Produktvorstellung mit Demo
- Roadmap zur Problemlösung
- Ganzheitliche Bewertung des Ansatzes
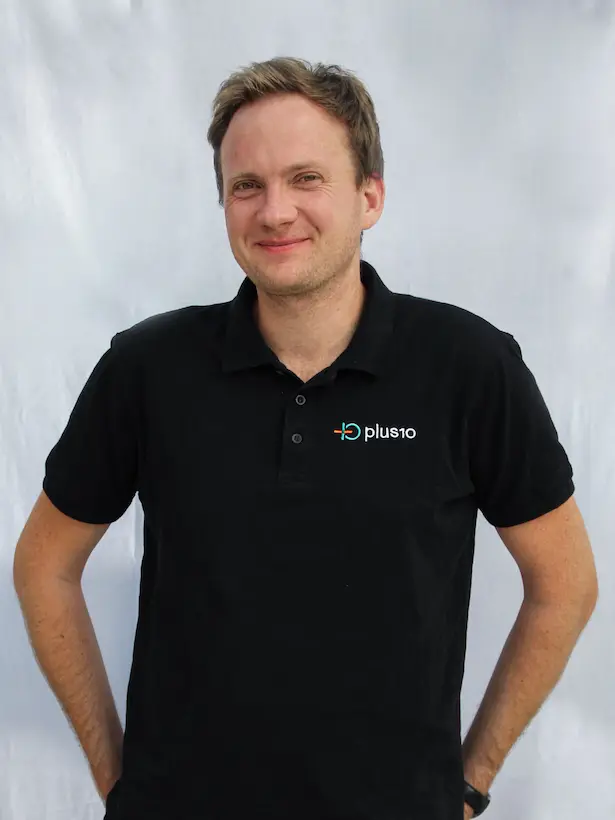