plus10 Software-Tools holen das Maximum aus bestehenden Fill- & Finish-Anlagen bei Schwarzkopf heraus
+ 17,4% Durchsatzsteigerung durch datenbasierte plus10-Optimierungssoftware identifiziert. An großen, vollautomatisierten und somit unübersichtlichen Fill- & Finish-Linien bei Schwarzkopf & Henkel erwies sich Shannon® und Darwin als besonders vorteilhaft.
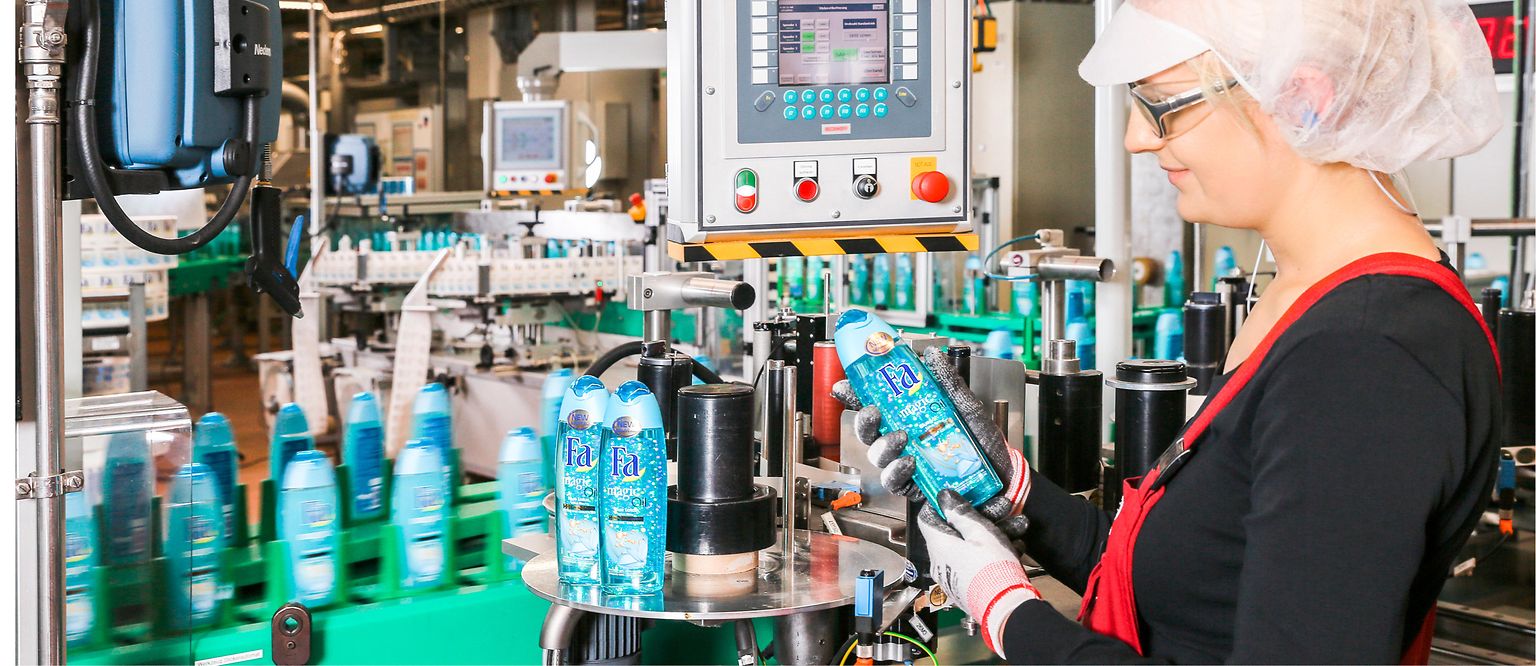